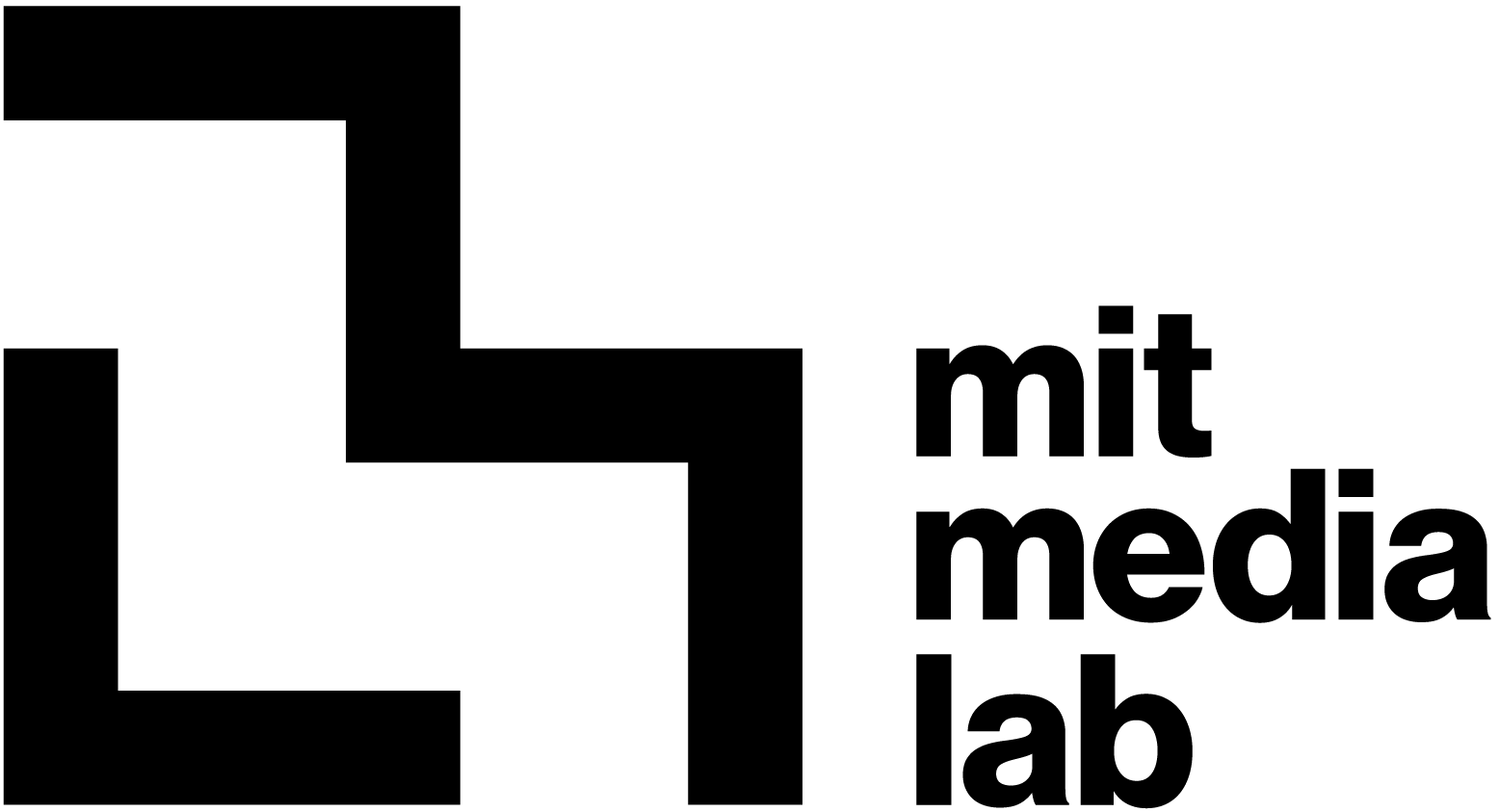
MIT Media Lab - Biomechatronics/Center For Extreme Bionics
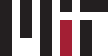
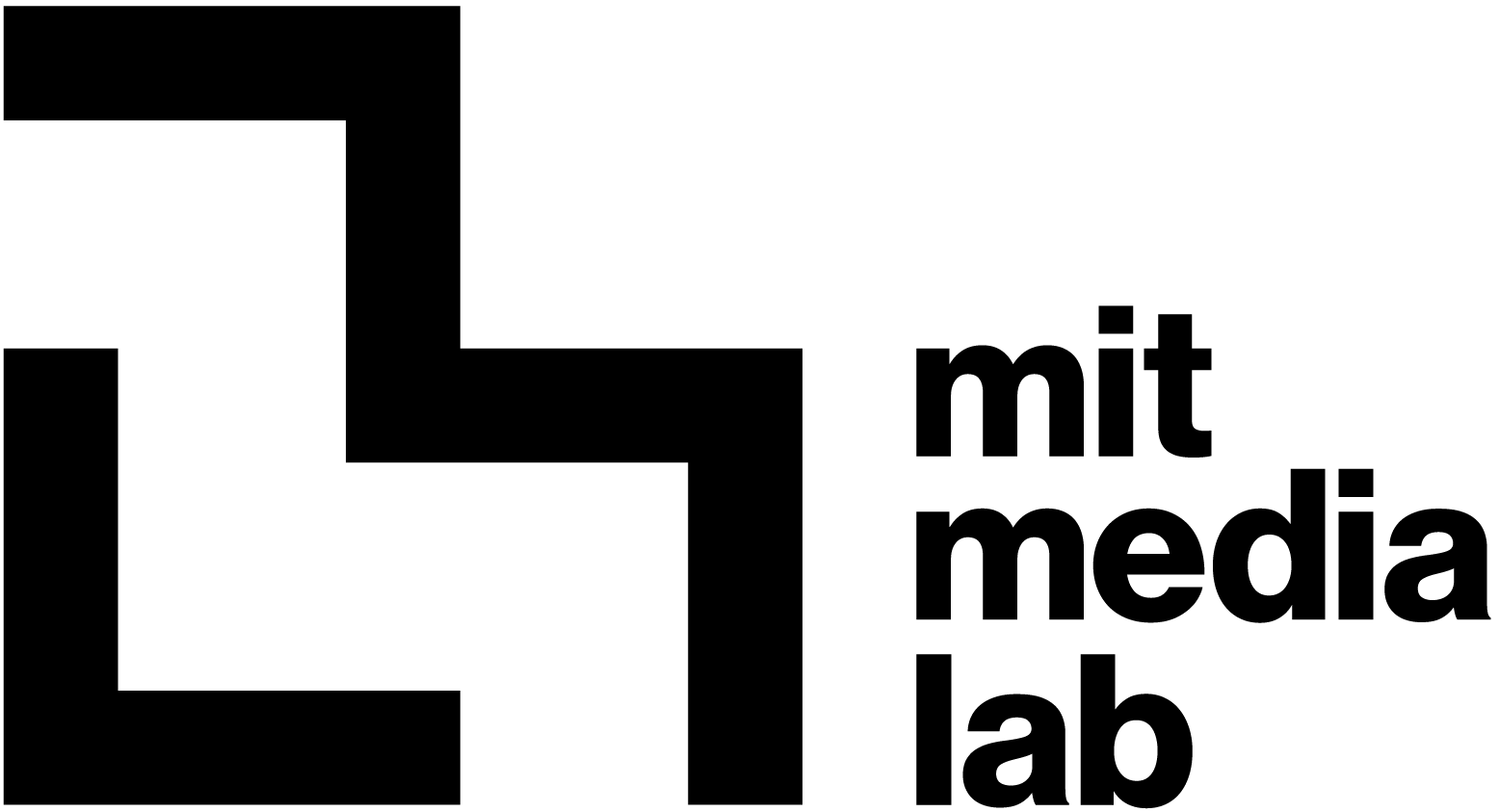
(2016 - present)
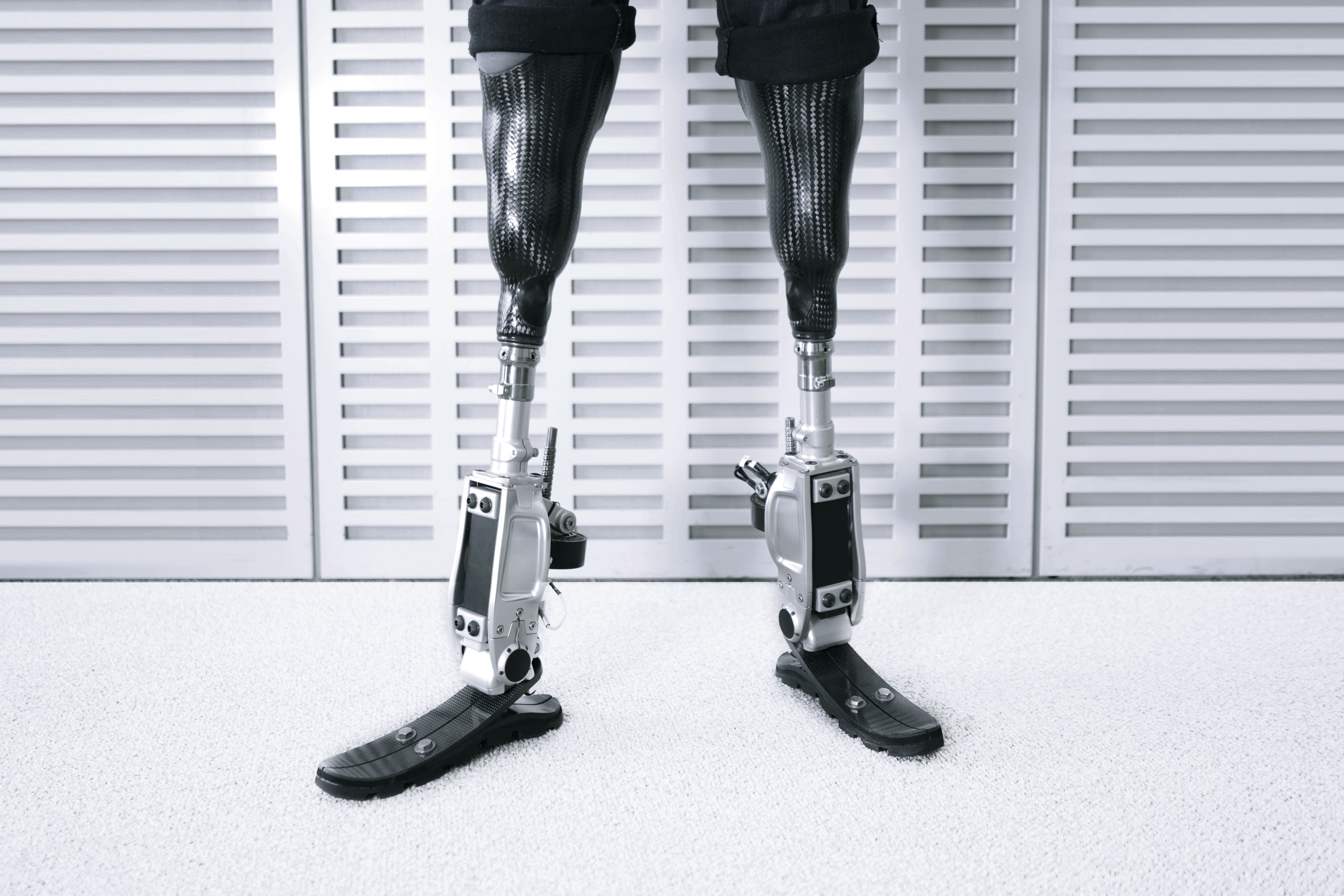
The image above shows the TF8 actuator I built for my PhD. This image was featured in the Amtrak Magazine, National (August 2018) in an article entitled "The Land of What If."
The U.S. Postal Service issued a 2020 Forever Stamp for Innovation and the image chosen to represent robotics innovation in the US is a picture of my PhD work, TF8!?!! Here is a MIT News Article New US postage stamp highlights MIT research. Also, you can buy the U.S. Postal Service 2020 Forever Innovation Stamp!
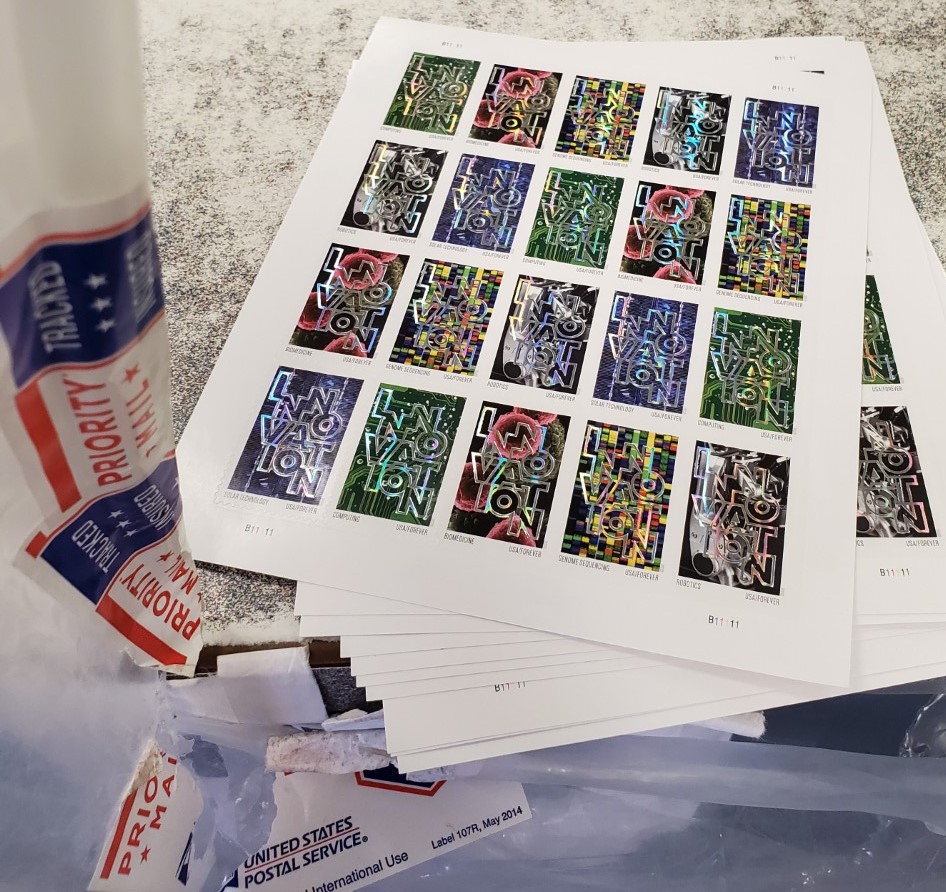
Bionic limbs are the ultimate humanoid robot, and so it is both an honor and perhaps the most appropriate innovation to show for robotics in 2020. Robotic prostheses integrate biomechanics, mechanical, electrical and software engineering. No piece of it is off-the-shelf, as to attempt to fit within the confines of the human form and to match the bandwidth and power density of the human body, we must push the bounds of every discipline: computation, strength of materials, magnetic energy densities, biological interfaces, just everything!
The image for the stamp was taken by Andy Ryan. Here is another one of the amazing photos he took of the actuators (copyright Andy Ryan)
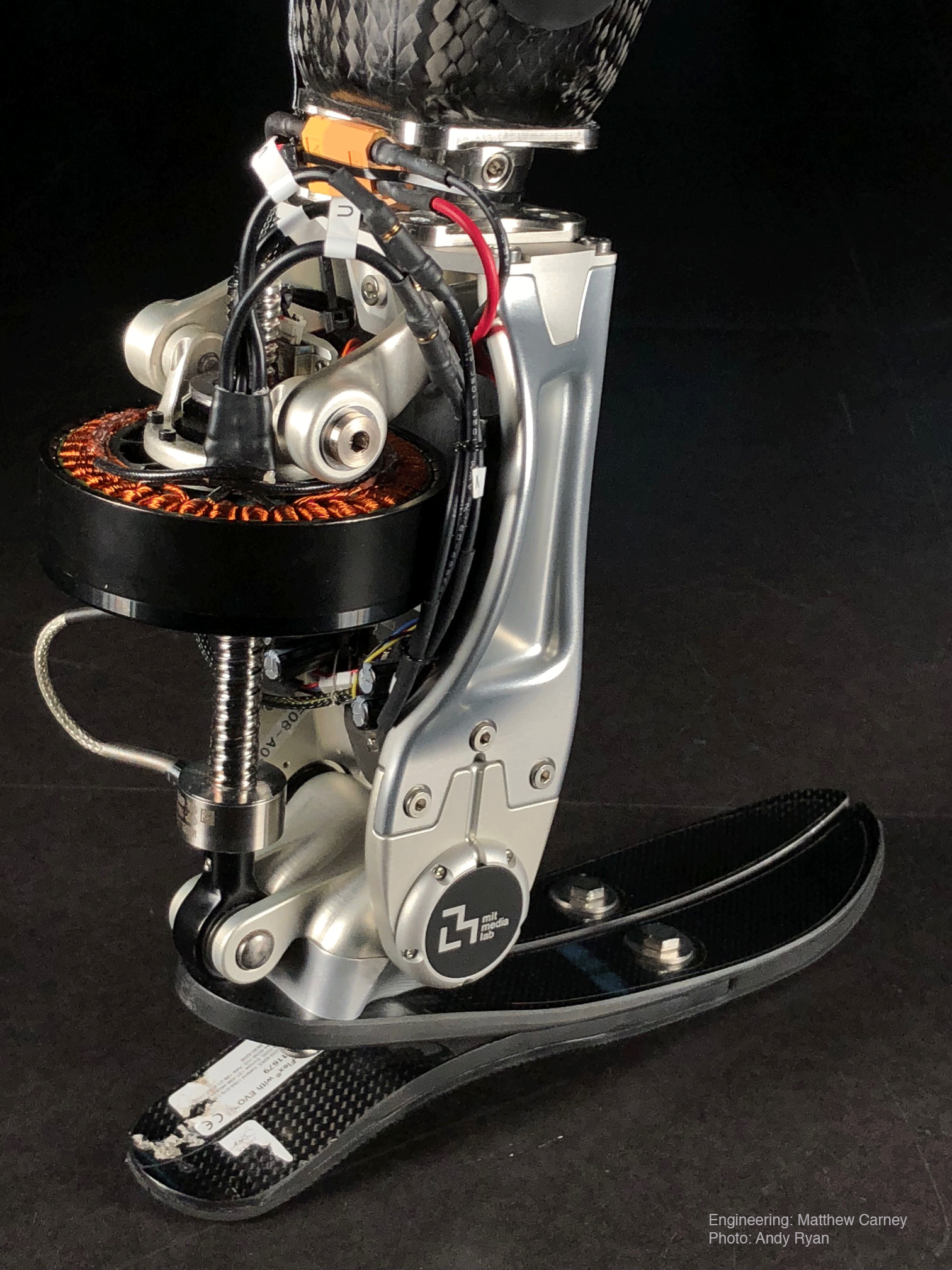
I mean, it's a freakin' honor to have my PhD work featured as a USPS Stamp. I collected stamps as a kid, and now to have my work featured on a Forever stamp is really an unthinkable honor: I hope this feat is an inspiration to young students everywhere to crush their homework to build the skills to make a positive impact on the world. It's important to recognize, though, that while I worked insane hours to build this thing -- and I mean, I put in ALL I had -- and really tried to inspire with its design as much as its engineering, it is truly the culmination of powered prosthesis work pioneered by Dr. Hugh Herr and our entire team at the MIT Media Lab Biomechatronics Group and it expands on work from a global community over more than a decade of development.
This is a video (below) walks through my process of making of the TF8 powered ankle prosthesis. It steps through each of the development processes from blank sheet of paper all the way through to walking (Sound On!).
I've been asked how long it took. Well from when I pulled out a blank sheet of paper to having a person walk was about 12 months. The breakdown is roughly:
- 6 months on the math/simulation (partially because I didn't know Matlab yet).
- 2 months sketching designs
- 1-2 months detailed design
- 1 week assembly (it actually went together the first time without problems -- thanks master modeling)
- 2-3 months programming, initial testing
- 1-2 years tuning controls and troubleshooting to eek out more performance.
What I love about working on powered prostheses is that it transcends the disciplines from engineering to healthcare to politics. It goes beyond tightly integrating neurally controlled power dense actuators that aim to replicate biological behavior; it gets to conversations about the brutal realities of private healthcare and the deeply personal experiences of our affected subjects. This work is profoundly American: the US military funds our research in the hopes to get their soldiers back to the battlefield, and yet politics severely limits our ability to deploy these advanced technologies by propagating a disjointed healthcare system that favors short-term cost savings over long-term outcomes and thus limiting the ability to scale the capital intensive production of the same robotic prostheses. Politics meets healthcare meets access to capital and technology!
There is nothing like 2020 to show exactly what I mean. We have the means, the technology, and the wealth to efficiently solve many health issues, and yet...we don't. What a year to receive a stamp, it is a defining stamp for a moment in history.
The actuator was designed specfically to demonstrate neural control of powered prostheses. However, it can also be controlled with relatively passive controllers, or with automated terrain adaptation. The video below is the result of PhD work from Roman Stolyarov which was the development of an automatied terrain adaptation controller for the leg.
And this is what my desk looked like, often, while developing this system. It's good to be an engineer!
TF8 Knee and Ankle Powered Prostheses
My PhD was the design, build, and control of a novel powered knee and ankle prosthesis - that means full development of the entire stack from math to working walking system. I outsourced development of the embedded system to Dephy, and procured custom modified motors and machined components from domestic and international manufacturers. I did machine a couple components but certainly left the bulk of it to the professionals. The technology is based on a series elastic actuator exploiting the biomimetic feature of series elasticity to extend the power delivery capacity of the motor as well as reduce overall energy consumption per stride. My process includes feeding gait data through dynamic equations in a kinematically clamped manner, to search for the optimal configuration of motor, spring, gear ratio. Further design refinements then include searching for optimal linkage geometry with the objective of achieving minimal energy consumption for each stride of walking gait.
Shown here is a simple walking controller based on a finite-state machine. It looks at joint torque, angle and velocity to determine where in stride the user is and from there to provide certain gait specific behavior at the joint.
The papers below describe the design process and hardware in great detail. Feel free to explore them can ask questions if you see fit.
PhD Dissertation Defense
Publications
- Carney, Matthew E. (2020) "Design and Evaluation of a Reaction Force Series Elastic Actuator Configurable as Biomimetic Powered Ankle and Knee Prostheses." PhD Dissertation, Massachusetts Institute of Technology.
- Carney, Matthew E., T. Shu, R. Stolyarov, J. F. Duval and H. M. Herr, "Design and Preliminary Results of a Reaction Force Series Elastic Actuator for Bionic Knee and Ankle Prostheses," in IEEE Transactions on Medical Robotics and Bionics, vol. 3, no. 3, pp. 542-553, Aug. 2021, doi: 10.1109/TMRB.2021.3098921.
- Carney, Matthew E., and H. M. Herr, “"Electric-Energetic Consequences of Springs in Lower-Extremity Powered Prostheses on Varied Terrain," 2020 8th IEEE RAS/EMBS International Conference for Biomedical Robotics and Biomechatronics (BioRob), New York City, NY, USA, 2020, pp. 989-996, doi: 10.1109/BioRob49111.2020.9224458.
- Stolyarov, Roman, Carney, Matthew E., and H. M. Herr, “"Accurate Heuristic Terrain Prediction in Powered Lower-Limb Prostheses Using Onboard Sensors," in IEEE Transactions on Biomedical Engineering, vol. 68, no. 2, pp. 384-392, Feb. 2021, doi: 10.1109/TBME.2020.2994152.
- Stolyarov, Roman, Carney, Matthew E., and H. M. Herr, “Automatic Incremental Learning of Terrain Transitions in a Powered Below Knee Prosthesis,” EngrXiv, DOI 10.31224/osf.io/zn3wf, 2020.
The First Human Steps on TF8
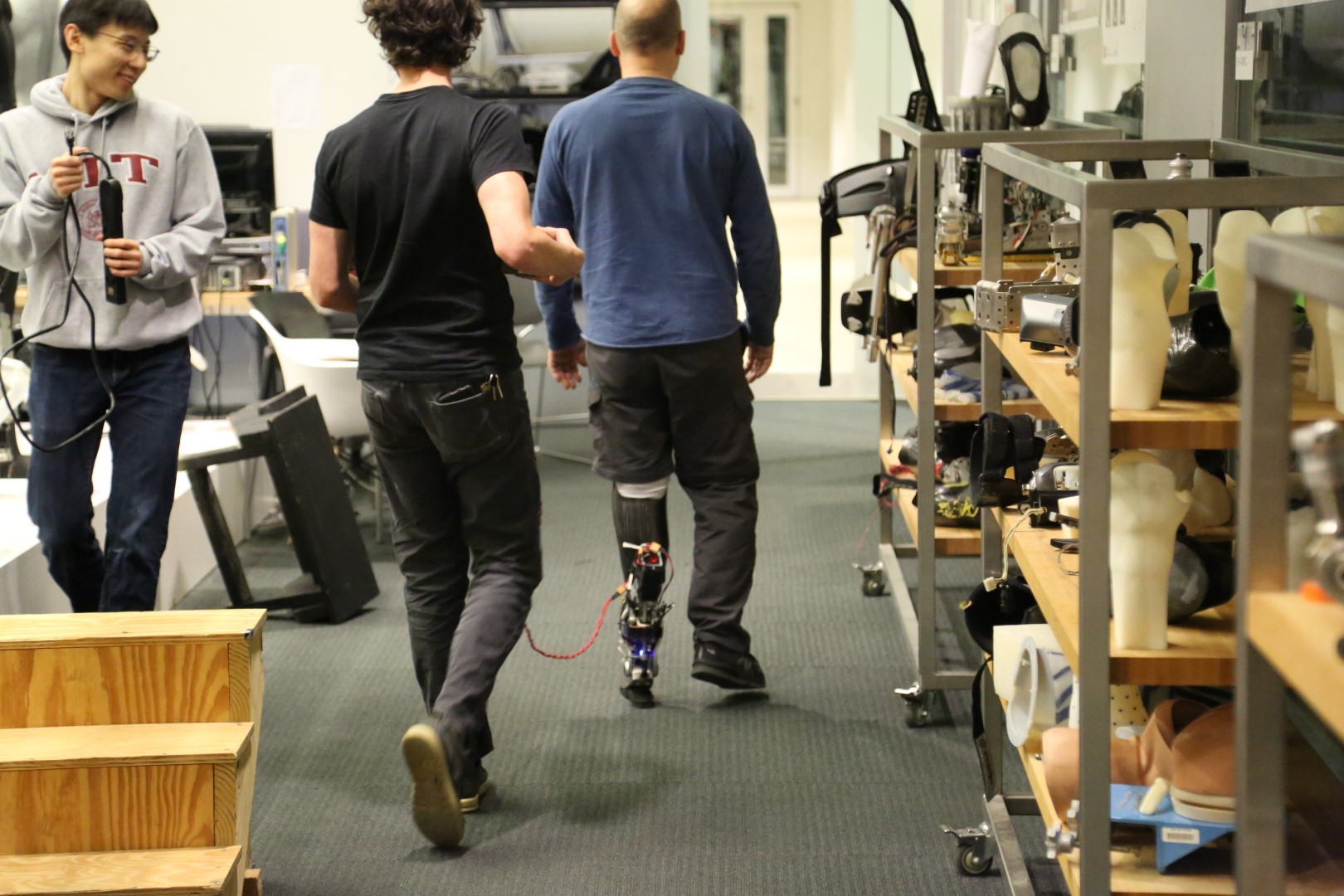
Over a dozen people have used the prosthetic knee or ankle actuators.
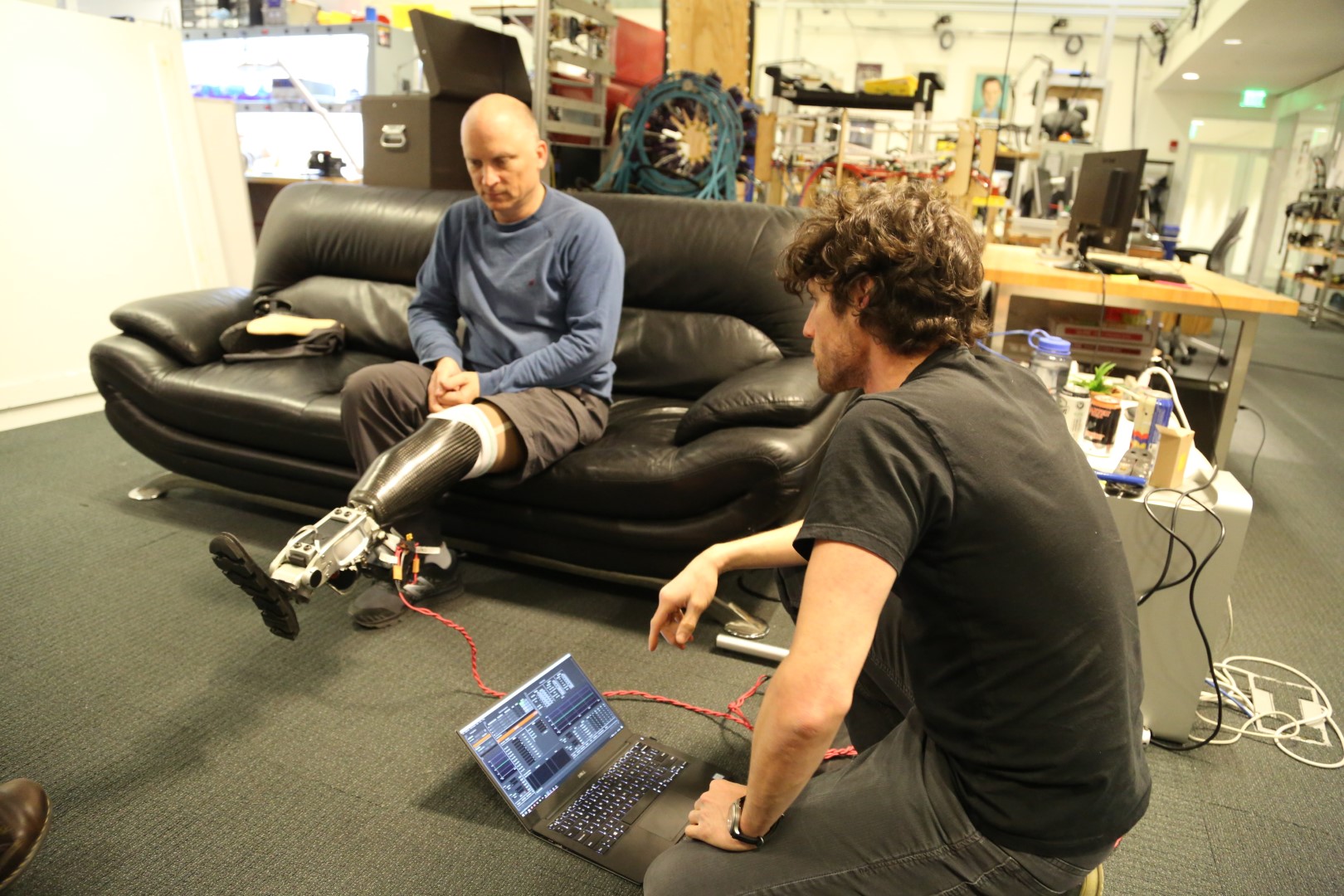
Testing with Dr. Herr
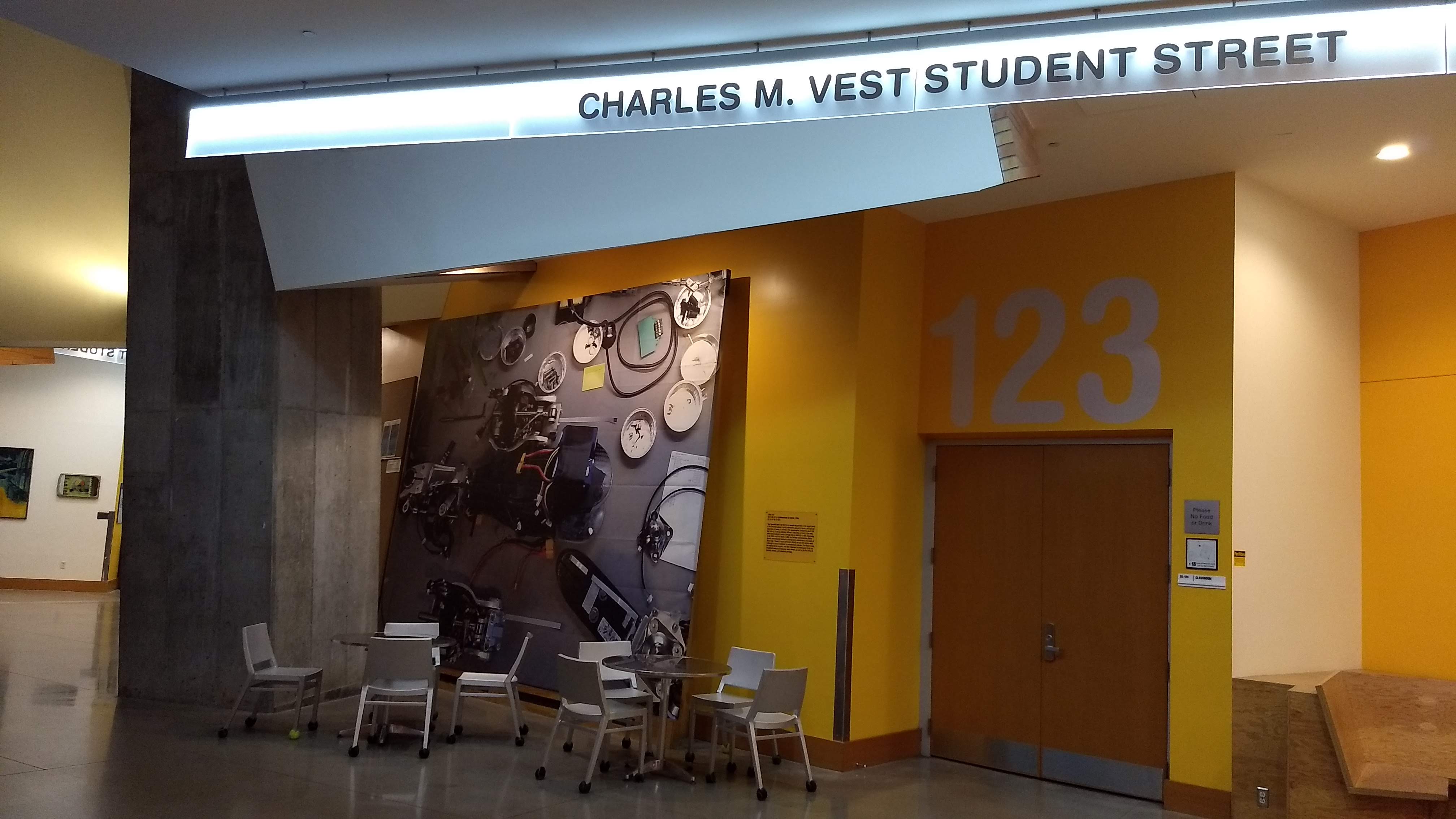
There's a giant picture of my desk on Stata Street in the MIT CSAIL building.